Showing 1 to 15 of 2394 results
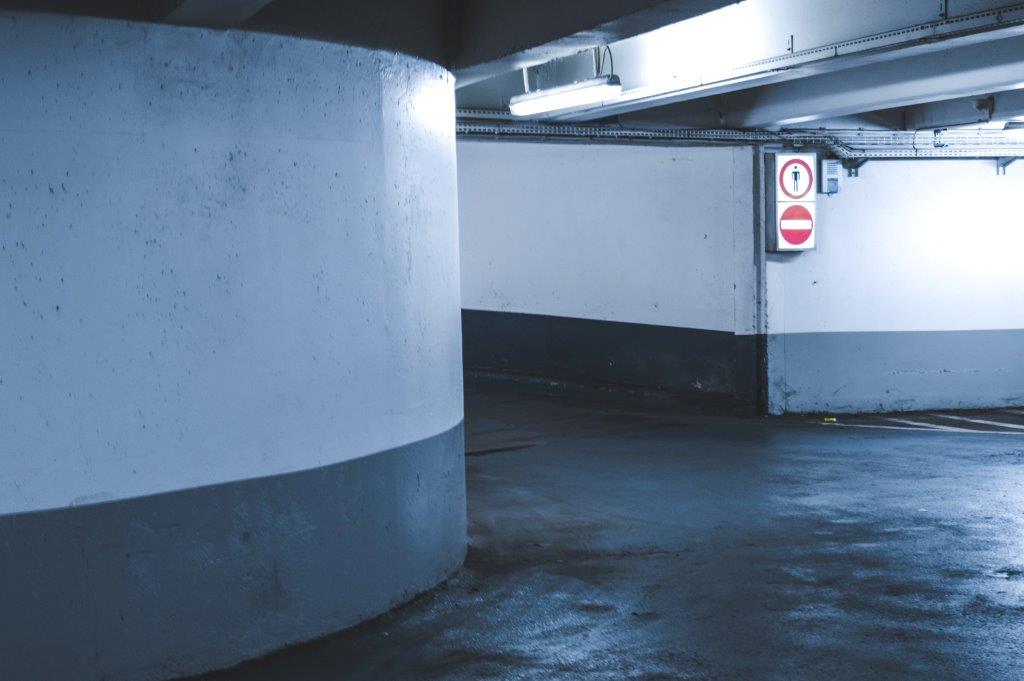
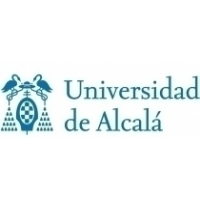
Artificial vision system for the semaphoric control of the access to parking and garages, through the monitoring of pedestrians.
Patents for licensing Universidad de Alcalá-OTRI
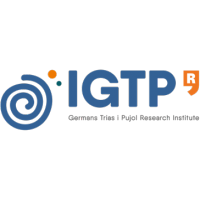
Drug Delivery Platform
Patents for licensing Germans Trias i Pujol Health Sciences Research Institute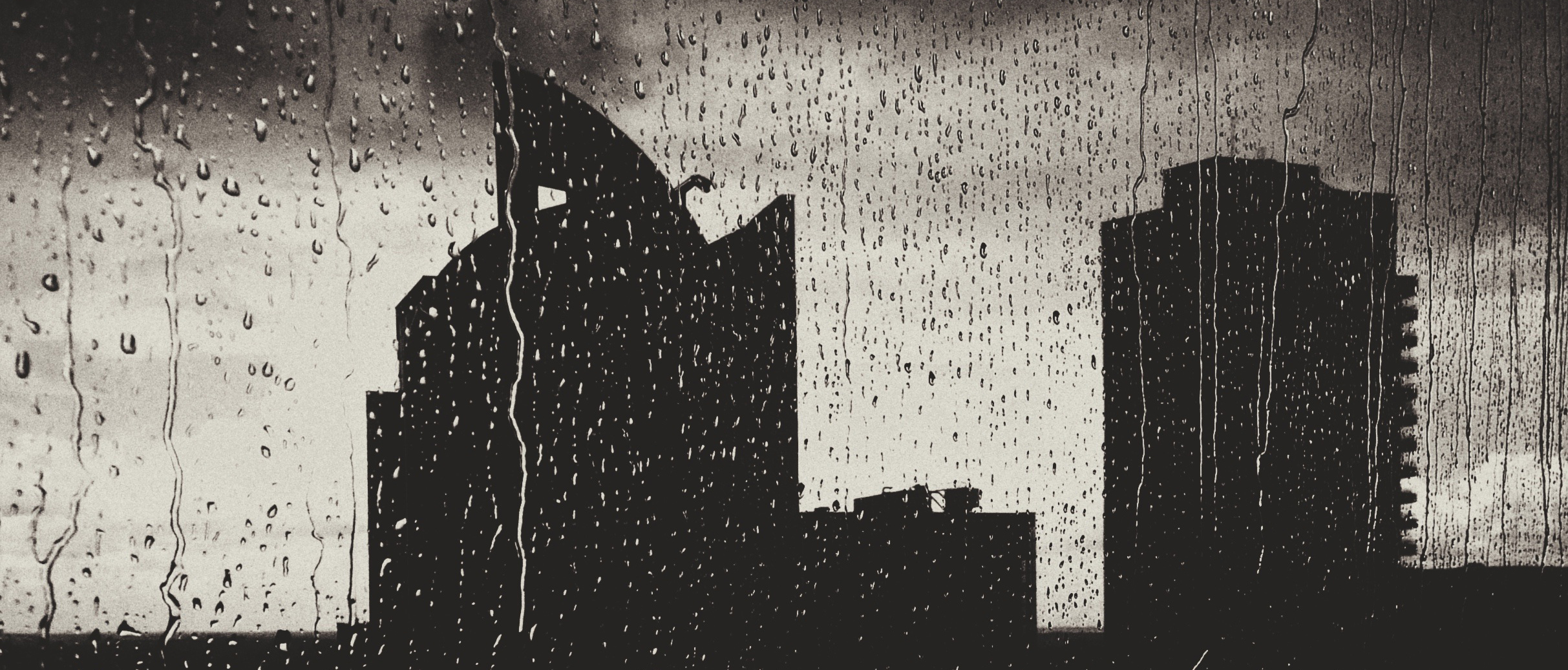
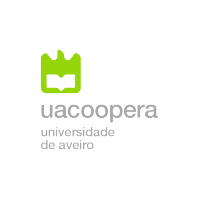
Removal of zinc from rainwater using a biomaterial
Innovative Products and Technologies UATEC - Unidade de Transferência de Tecnologia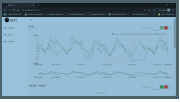
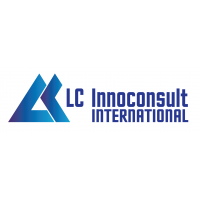
BAT - autonomous Batch Analytics plaTform
Innovative Products and Technologies Laser Consult Ltd.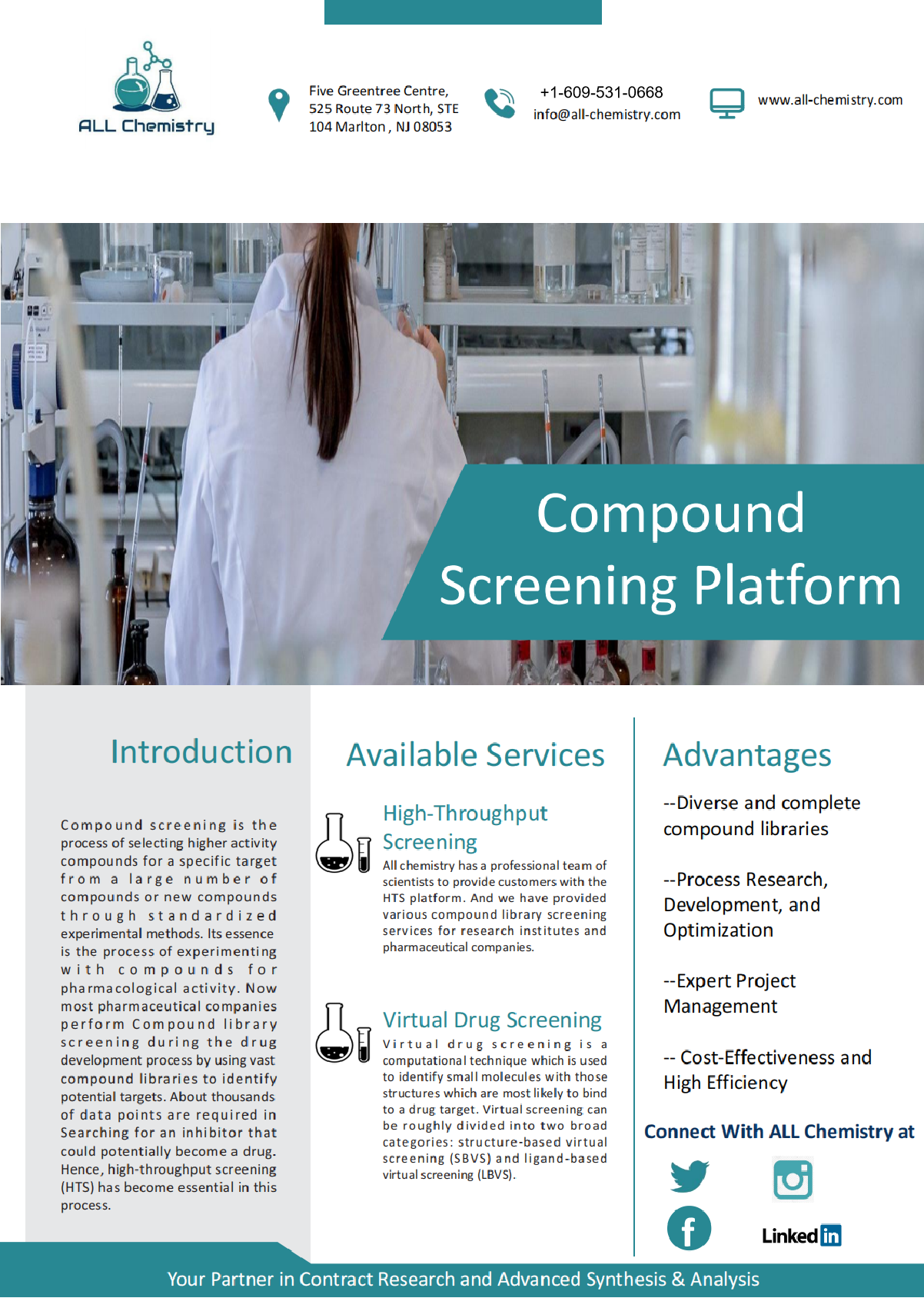
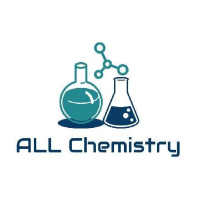
ALL Chemistry Inc.'s High-Throughput Screening Service
Research Services and Capabilities ALL Chemistry Inc.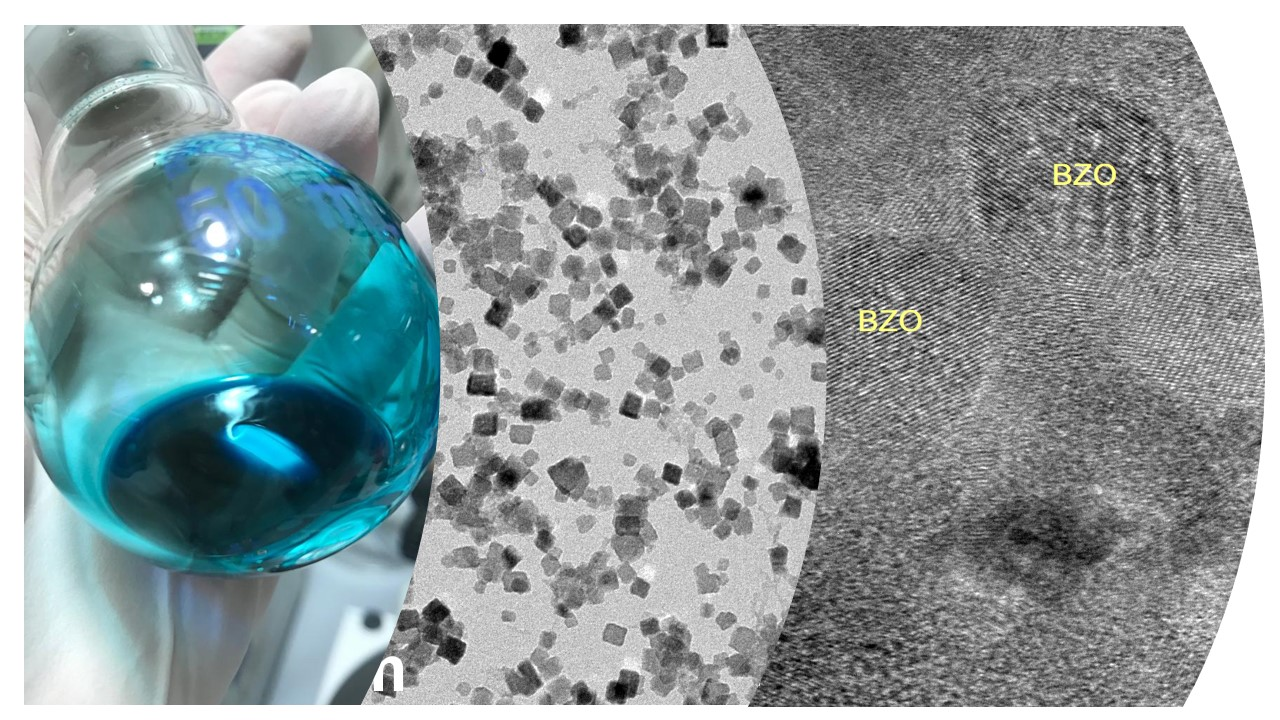
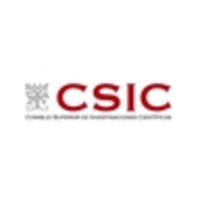
Ink for the production of superconducting flexible tapes
Patents for licensing CSIC - Consejo Superior de Investigaciones Científicas
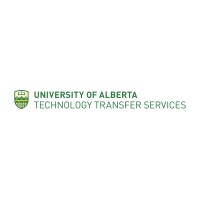
Unconjugated PLGA Nanoparticles in the Diagnosis and Treatment of Alzheimers Disease
Innovative Products and Technologies University of Alberta, Technology Transfer Services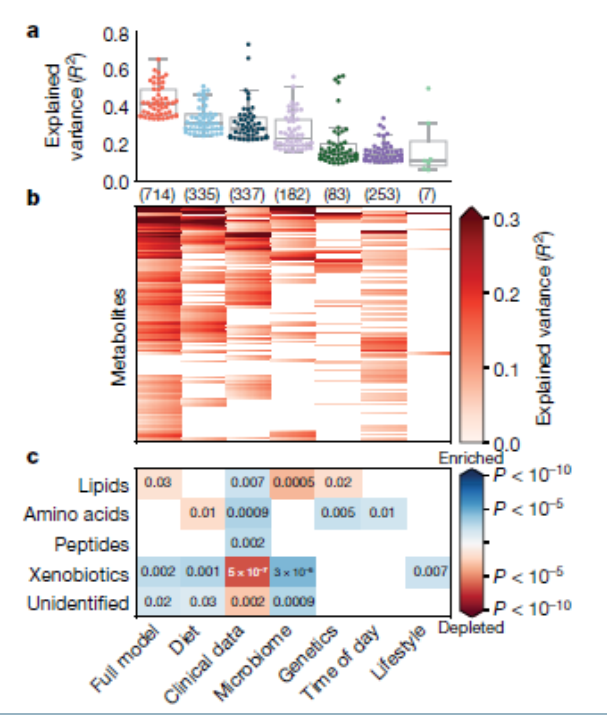
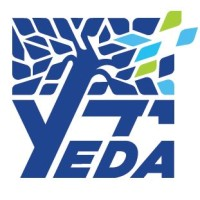
Predicting Blood Metabolites
Patents for licensing Yeda![A Sustainable SAGD Follow-up Steamless Enhanced Bitumen Recovery Approach Combined with Non-Condensable Gas and Waste Heat Utiliza[…]](https://static7.innoget.com/uploads//018987689ea9b28bbcdc81e98ebbfb87bc68250e.png)
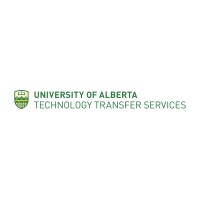
A Sustainable SAGD Follow-up Steamless Enhanced Bitumen Recovery Approach Combined with Non-Condensable Gas and Waste Heat Utiliza[…]
Patents for licensing University of Alberta, Technology Transfer Services
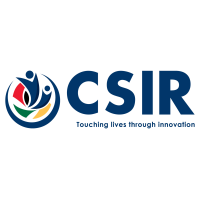
Isinkwe
Innovative Products and Technologies CSIR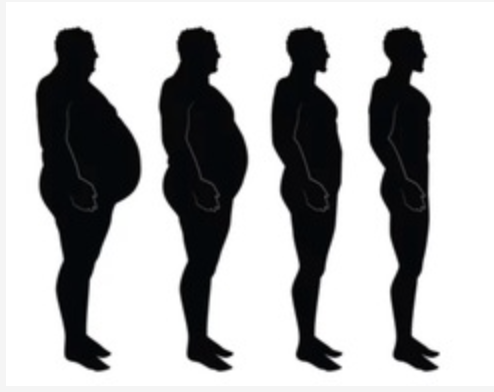
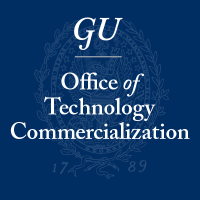
Treatment of Metabolic Syndrome and Obesity
Innovative Products and Technologies Georgetown University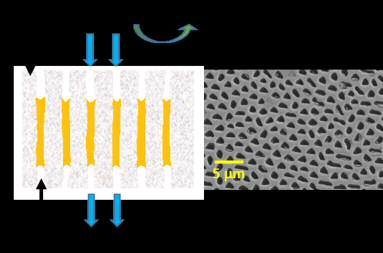
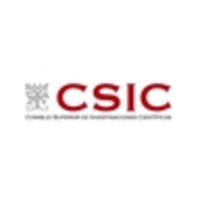
Ceramic membrane with highly aligned pores for CO2 separation
Patents for licensing CSIC - Consejo Superior de Investigaciones Científicas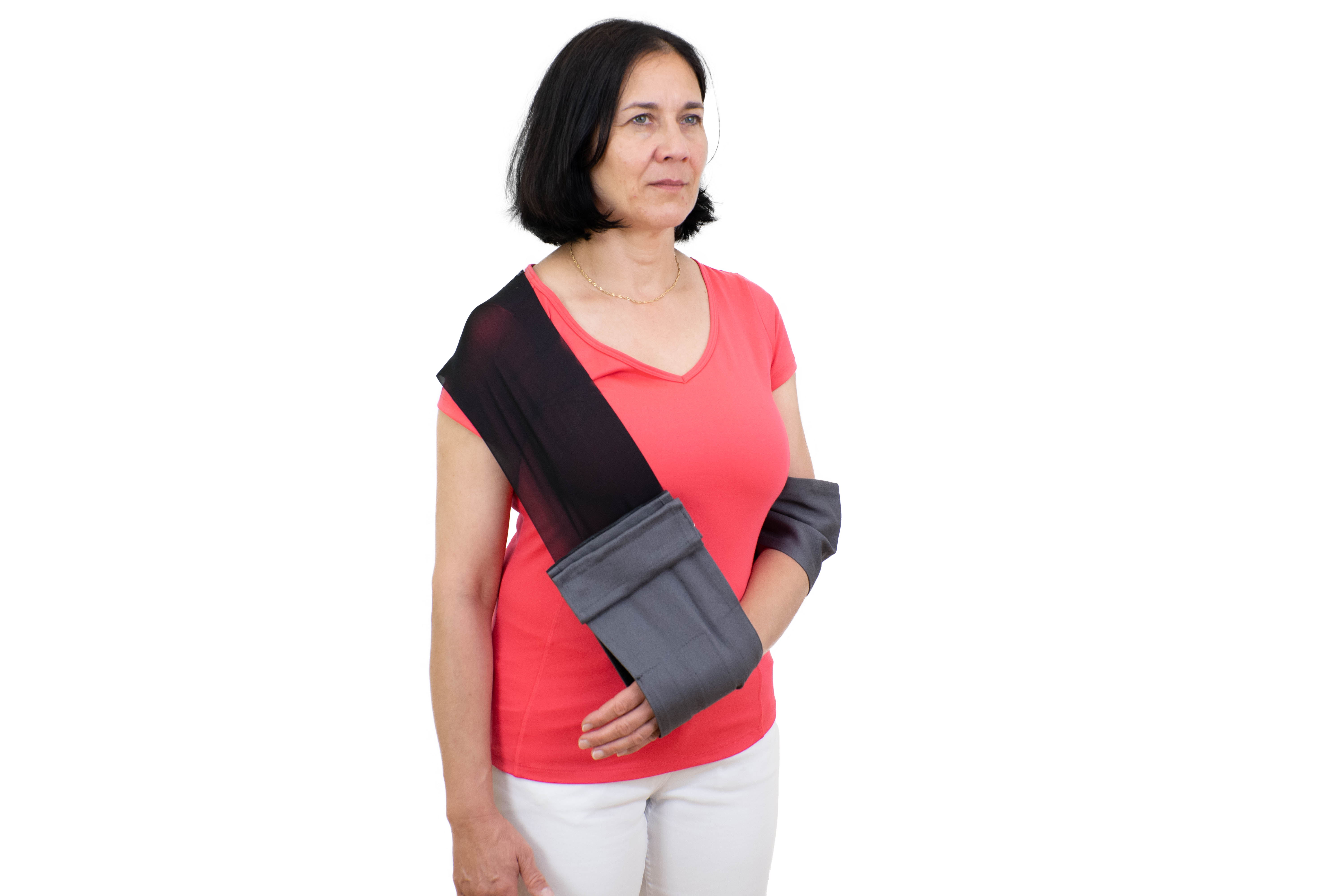
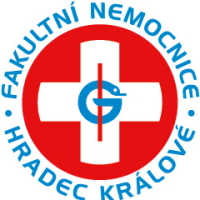
Sling for paretic limb - Special aid for patients after stroke or brachial plexus injury
Innovative Products and Technologies University Hospital Hradec Králové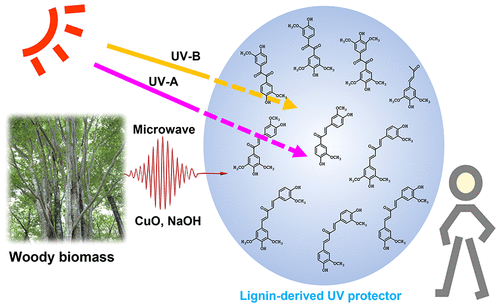
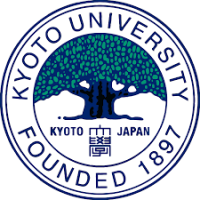
Next-Generation Lignocellulosic Materials
Innovative Products and Technologies Kyoto University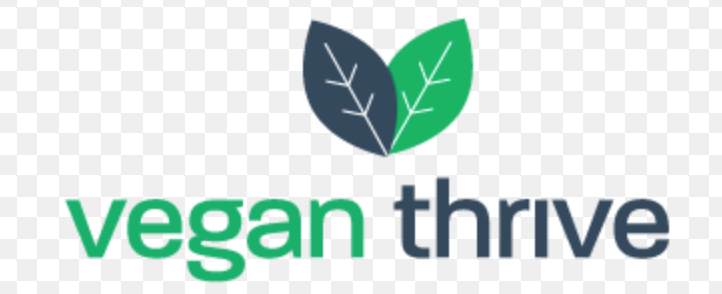
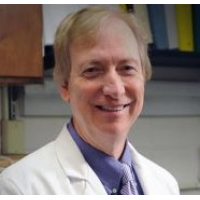